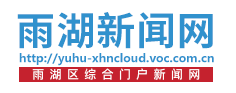
雨湖融媒7月8日讯(通讯员 廖敏昱)中国兵器江南工业集团坚持质量至上,立足科研生产实际,创新构建“四优三必须”工艺提升机制。该机制以“落实设计要素优、指导现场操作优、工艺风险管控优、工艺设计标准优”为核心目标,以“生产要素必须覆盖、工艺优化必须验证、过程风险必须辨识”为硬性要求,通过双向驱动模式实现工艺全流程、全要素、全层级管控,有效提升质量管控与生产效能,为企业科技创新转型筑牢根基。
构建设计工艺协同机制,夯实产品质量源头根基。面对产品设计来源多元、工艺早期介入不足的困境,公司分类施策,构建差异化协同模式。针对系统内院所主导项目,创新采用“培训 + 验证”双轮驱动机制,累计开展100余次设计人员现场培训,组织2200余人次工艺人员参与交流,成功保障10余型产品科研试制及多型产品定型生产,确保工艺精准诠释设计意图。针对院企合作与自主设计项目,推行“论证 + 审查”全过程协同,工艺师从方案设计阶段深度介入,开展工艺性审查与关键工序控制。在某型号项目中,通过协同建设防护涂装生产线,显著提升产品生产安全性、质量一致性与保供能力,实现设计与工艺的深度融合。
实施上下联动工作机制,提升工艺执行应用效能。为强化工艺文件实操性,公司构建三级联动管理体系。成立专项清查小组,制定年度提升计划,组织各生产单位围绕“人、机、料、法、环、测”六大要素,系统排查工艺问题。机制运行以来,累计清查完善1500余份工艺文件,解决800余项工艺难题,推动工艺设计与生产实践深度对接。在工艺验证环节,建立“基层验证 + 专家评审”双轨制,技术人员驻场与操作人员协同验证优化方案,关键工序变更需经用户代表认可。如针对焊接导线工序实施防错设计验证,有效规避操作风险。同时,通过月度工艺纪律检查,建立问题反馈 - 改进 - 验证闭环,确保工艺要求100%落地执行。
强化风险辨识管控机制,筑牢生产质量安全防线。公司以全流程风险防控为目标,构建“四维一体”风险管控体系。坚持问题导向,组织跨部门团队围绕生产全流程,从六大要素入手,系统梳理质量与安全风险,形成工艺风险辨识清单。以典型产品为试点,探索标准化辨识流程并推广至全产品线,实现100%产品覆盖。通过全员参与模式,组织生产各层级人员协同制定管控措施,经专业评审后发布实施。建立动态更新机制,根据生产条件变化实时补充风险点,确保实现产品全生命周期风险可控。机制运行以来,识别某攻坚产品风险点100余个,制定管控措施200余项,有效提升生产本质安全水平。
推进工艺标准建设机制,实现精益管理降本增效。针对工艺设计标准化需求,公司开展“双轮驱动”标准化建设。在刀具管理领域,依据国际国内标准和行业惯例,组织机加单位开展刀具型号统计,编制统一编码规则,实现同规格刀具“一码到底”,有效杜绝重复采购,大幅提升刀具管理效能。在工艺模板优化方面,组织技术骨干优化工艺模板,细化技术参数、操作要求等填写规范,并新增含设备、刀具代码等信息的“加工清单”,推动工艺设计更精准。坚持“试点先行、全面推广”,通过重点项目验证优化后形成固化模板。此举不仅规范了生产流程,更通过刀具统型与模板细化,为企业节创价值150余万元,显著提升工艺设计质量与管理效能。
健全学用贯通培养机制,增强工艺创新发展动能。为破解工艺标准执行难题,公司构建“三维学习”成长体系。通过集中培训、案例研讨、经验分享等多种形式,组织工艺人员系统学习标准规范,累计开展专题培训50余场,覆盖人员1800余人次。邀请科技骨干组建内训师团队,编制典型案例集,促进知识经验共享。建立“学用结合”考核机制,将理论知识与实际应用挂钩,推动工艺人员形成系统知识体系。工艺提升机制实施以来,通过运用所学经验作法、创新技术等,实现降本增效收益183万余元,有效提升工艺设计体系化能力与创新水平,为企业高质量发展注入强劲动力。
责编:易阳思
来源:江南工业集团
乐之书店“如约而至”:静享阅读时光,尽享诗意人生
视频丨万楼·青年码头,传统与现代交相辉映,让老湘潭焕发新活力!
文旅专题丨一路芬芳 经典雨湖
专栏丨雨湖文苑
义源当铺思“秋”
视频丨穿越时空的风情 唤醒传统街区的温情记忆 风车坪文创街区举行汉服快闪秀
张岱:老窑湾筷子巷纪事
张岱:今昔唐兴街
下载APP
分享到